티타늄 합금분말을 사용한 3D프린팅 부품은 정밀한 설계제어가 가능 하고, 가벼우면서도 내구성이 강해 자동차, 항공우주, 의료용 임플란트 등 금속 3D프린팅 부품 소재의 52%를 차지한다.
생기원 기능성소재부품그룹 박형기 수석연구원팀은 나노입자를 티타늄 분말 내에 균일하게 분포하는 방식으로 소재 성능을 강화한 차세대 금속 3D프린팅 분말소재 기술기반을 확보했다.
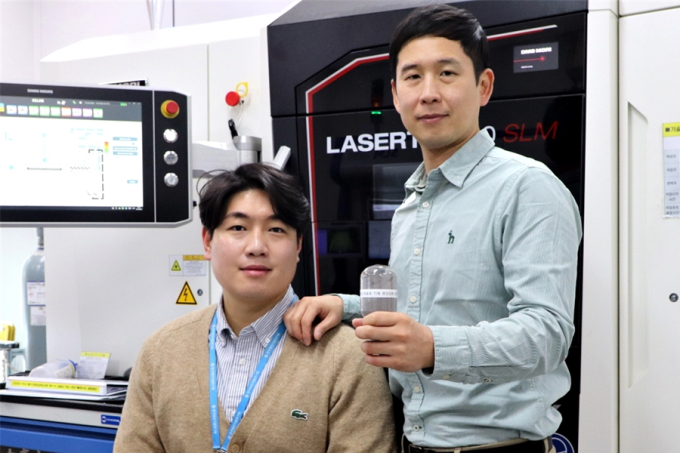
금속 3D프린팅 부품은 합금분말을 적층하고 레이저로 녹이면서 성형하는 과정을 거쳐 만들어 지는데, 복잡한 형상의 부품도 바로 제조할수 있어 시간과 비용을 단축할 수 있다.
반면 합금분말이 급속 응고되거나 열이 빠져나가면서 부품 내부에 기공이나 크랙이 발생하는 단점이 있어 레이저 출력 조절로 변수를 제어하는 방식으로 결함을 줄이는 연구가 진행 중이다.
연구팀은 레이저로 변수를 제어하는 연구방식에서 3D프린팅에 최적화된 차세대 복합소재 분말을 개발하는 전략으로 발전시켰다.
복합소재는 금속분말에 나노미터 크기의 미세한 나노 세라믹 물질을 분산시켜 강도를 높인 소재로, 3D프린팅에 적용하면 응고되는 과정에서 분산된 나노입자 표면에 핵 생성이 활발해지면서 견고한 미세조직이 형성된다.
하지만 기존 3D프린팅용 복합소재 분말은 금속분말 표면에 나노입자를 접착시키는 방식이기 때문에 입자가 균일하게 분포되지 않고 분말 유동 과정 중 나노입자가 분리돼 재사용이 어려운 단점이 있다.
연구팀은 이같은 한계를 3D프린팅 공정에 최적화된 소재 개발로 극복하고자 열역학 기반 시뮬레이션으로 티타늄과 나노입자 조성을 선정했다.
이를 바탕으로 티타늄-나노입자의 최적 조성과 비율을 선정하고, 나노 입자를 티타늄 분말 내부에 ‘in-situ’로 일체화하는 제조공정을 설계했다.
연구팀은 in-situ 기법으로 40~50㎚ 크기 나노입자를 티타늄 분말 내부에 분포시키는 제조기술 개발에 성공했다.
in-situ로 합금한 분말은 이전 ex-situ 방식과 비교해 나노입자가 균일하게 분포돼 3D프린팅에서의 결함을 줄일 수 있고, 제조 과정에서 나노입자가 튕기지 않아 별도 처리과정 없이 100% 재사용할 수 있다.
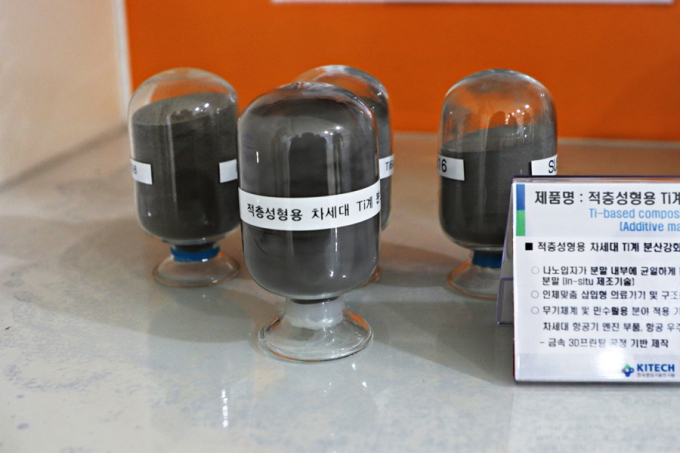
박 수석연구원은“나노입자 일체형 티타늄 분말을 사용하면 3D프린팅 부품의 기계적 특성과 신뢰성이 모두 향상시켜 향후 3D프린팅 기술의 핵심 소재로 활용될 것”이라며 “다양한 산업의 티타늄 부품에 적용 가능해 금속 3D프린팅 세계시장을 선점할 수 있다”고 밝혔다.
대덕특구=이재형 기자 jh@kukinews.com